The 5 Whys Technique: When Is It Used?
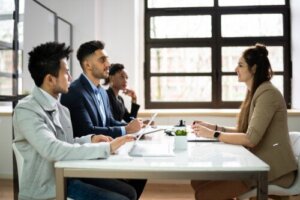
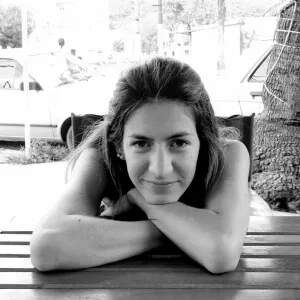
Written and verified by the psychologist Maria Fatima Seppi Vinuales
Today, we would like to highlight the advantages of the 5 Whys technique, a method that explores the origin of conflicts. Specifically, it examines their underlying cause-and-effect relationship.
In other words, this is a tool that allows the group participation of different actors involved to follow up on the causes until the origin of the problem is reached. Since it doesn’t require a lot of resources for its application, it’s widely used in different work environments. Let’s take a closer look at what it’s all about.
What is the 5 Whys technique?
“The 5 Whys” is a problem-solving technique, created by Sakichi Toyoda, which began to be applied in the Toyota car factory with the aim of optimizing production. In particular, it aims to discover what are the obstacles that delay or prevent performance improvement.
This is a method that seeks to go beyond the apparent causes. It consists of asking 5 whys about a problem. In this way, it aims to get to the root to understand that there is what works as a cascade effect and triggers or maintains the rest of the problems.
Thus, once the origin is identified, it’s possible to intervene to change the situation. It is a technique recommended for finding causalities, not at a conception or development stage.
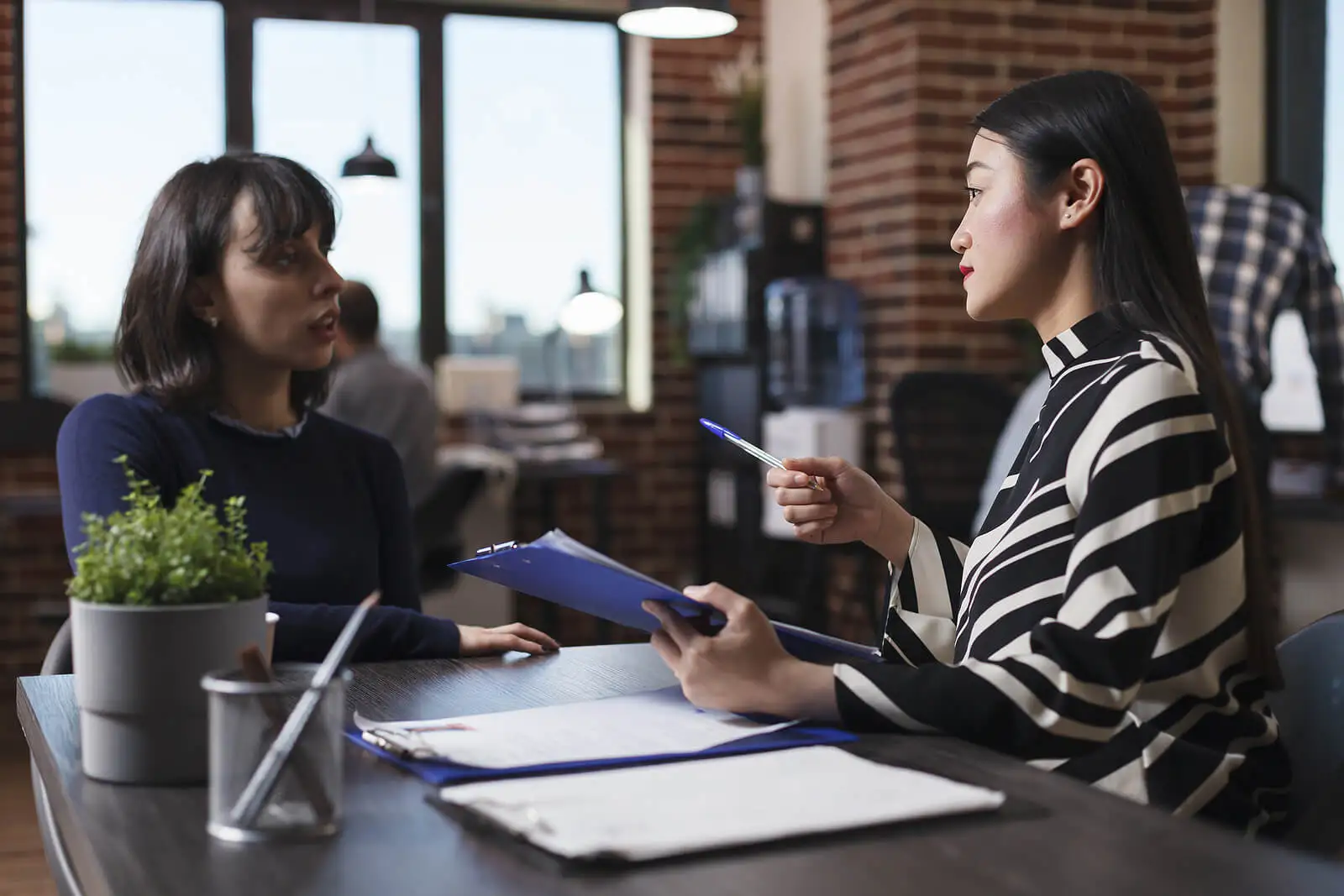
Like this article? We think you may also like to read: Social Darwinism: An Idea that Should Never Have Existed?
Importance and benefits of the 5 whys technique
Through the 5 whys technique, the entire chain of results between cause and effect is explored. This brings with it several benefits. We’ll tell you all about them below.
This technique xplores different causes and solutions
As you begin to investigate different causes, difficulties, and obstacles arise that have to do with multiple issues. In this way, it’s not a linear reading, but can be enriched with different components.
With this, there’s a greater chance of being able to make adjustments and succeed in the solutions or improvements implemented.
It provides an overview of the problems
This technique does not reduce a problem to an immediate cause. By exploring all its complexity, it provides a holistic view and therefore leads to more optimal solutions.
It’s easy to apply
Another advantage has to do with how easy it is to do. By asking simple questions, it’s possible to clarify an issue that perhaps no one had thought about before.
What should be taken into account is that it’s necessary to talk to the right people who know about the processes and who have an active part in it to use their knowledge.
It improves the well-being of employees
The fact of being interested in implementing improvements in the workplace isn’t only due to productivity at an economic level. However, it’s also about improving the well-being and motivation of employees. This prevents labor problems, which later lead to absenteeism.
How to apply the 5 Whys technique to your problem-solving
To apply the 5 Whys technique, it’s a good idea to set up a working group so that you can have a collective vision and different points of view on the origin of the problem. Then, start asking the questions.
From the different whys that arise, it’s possible to think of a kind of diagram that allows visualizing the causes. It’s a good idea to use a blackboard so that everyone can visualize it and, above all, so that everyone can contribute to new causes or focal points of the conflict.
Then, the most urgent and necessary interventions become a priority. This is because it’s not possible to address everything at the same time. Of course, once you decide on the course of action, you’ll have to implement the changes and monitor their impact.
It is also a good idea to explain why you’re using this technique and reassure those involved. This is not a tool that seeks to blame, but instead to understand how and why things work the way they do.
However, note that although this is a question of whys, the essential thing is to be able to find the cause. Sometimes this means asking for more or less than that number. At the same time, it’s necessary to know how to identify which answers to dwell on and which ones to go into a little more depth.
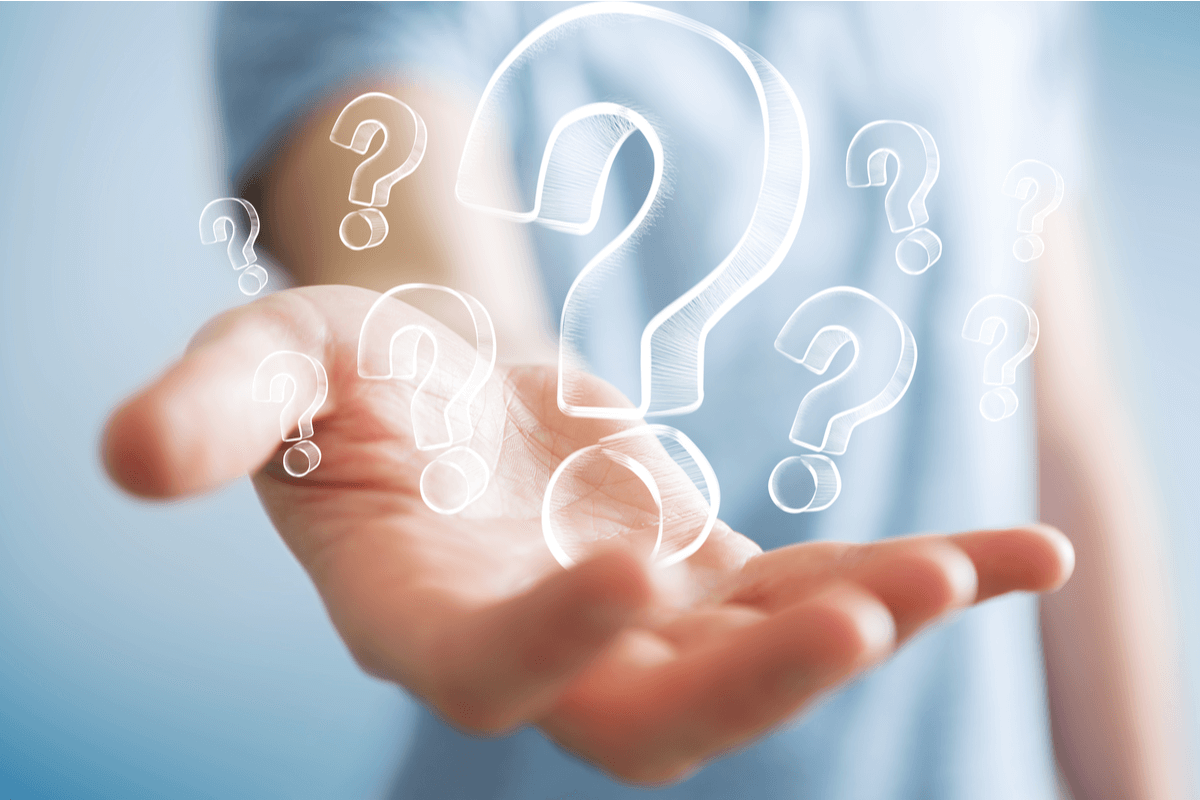
Examples of how to apply the 5 Whys technique
Here are some examples of how to use the 5 Whys technique
Example n°1
- Why do employees fail to submit their reports on time? Because they have too many meetings a day.
- Why do they have so many meetings a day? Because they have to share the progress of their activities.
- Why do they have to share the progress of their activities? Because they don’t have a communication and information management system in which they can upload their progress.
- Why don’t they have a communication and information management system where they can upload their progress? Because there has been no investment in creating one.
- Why has there been no investment? Because the area does not believe it’s necessary to change its processes.
Thus, from this “back and forth” of questions, you can infer that the cause is the fact that the work area does not consider it necessary to modify its processes to make them more efficient.
So, by knowing what is the cause that prevents better performance, it’s possible to think about solving it in some way and improving the organization.
Example n°2
- Why are there so many customer complaints? Because there are delays in the delivery of products.
- Why are there delays in delivery? Because there’s no way to assemble the packages on time.
- Why is there no way to assemble the packages on time? Because we’re understaffed.
- Why are we understaffed? Because Human Resources did not initiate a search process.
- Why didn’t they? Because they’re also understaffed.
Here, it’s also possible to identify the reason for the delays that impact the quality of service. Also, you can identify what you can do about it.
We think you may also like to read this article: Money Obsession: What Is It and How to Deal With It?
The importance of implementing changes
After consulting people about the causes and problems that prevent better performance in the workplace, it’s important to be consistent and implement the necessary changes.
Otherwise, there’s often a feeling that it’s all a “farce” and people lose motivation and become reluctant to collaborate on subsequent occasions.
For example, the postulates of the Lean philosophy, which consists of eliminating everything that is not necessary and that does not generate value, can be a good way to face changes in management.
Whatever the path to follow, it’s also necessary to consider the reality and the corporate culture. This is because some measures are not always relevant or possible.
All cited sources were thoroughly reviewed by our team to ensure their quality, reliability, currency, and validity. The bibliography of this article was considered reliable and of academic or scientific accuracy.
- Card, J. A. (2016). The problem with “5 whys”. BMJ Quality and Safety. 26:671-677. DOI: 10.1136/bmjqs-2016-005849
- Serrat, O. (2017). The Five Whys Technique. In: Knowledge Solutions. Springer, Singapore. https://doi.org/10.1007/978-981-10-0983-9_32
- Catalán, J. P., & Aparisi, M. G. (2019). Análisis de causa raíz. Técnicas y relación con los sistemas de gestión y las no conformidades.
This text is provided for informational purposes only and does not replace consultation with a professional. If in doubt, consult your specialist.